Unilin Technologies owns more than 3,800 patents across 500 families and continues to transform the flooring industry. Traditional SPC flooring production faces major problems with high scrap rates and misaligned bevels. Their new pressed bevel system provides a game-changing solution. This patented technology creates floors with unmatched precision and sustainability.
The system optimizes bevel appearance and depth without compromising the locking performance. Their state-of-the-art technology builds on previous successes, including the award-winning Unigrout technology that creates authentic ceramic-looking rigid floors. This technical overview shows how their next-generation pressed bevel system streamlines manufacturing processes and raises quality standards.
Technical Architecture of Next-Gen Pressed Bevel System
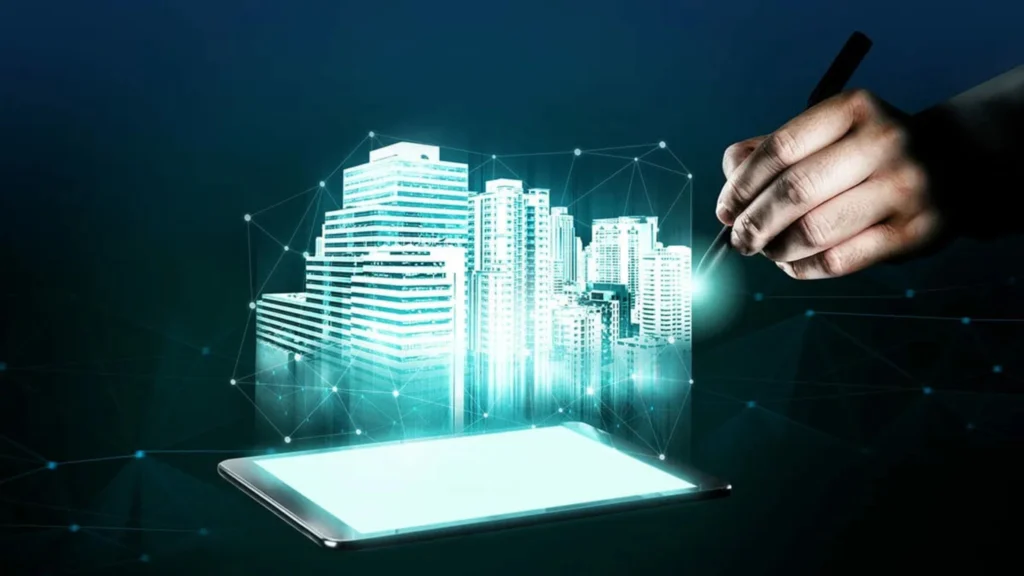
The next-generation pressed bevel system marks a major step forward in flooring technology. We focused on boosting precision and making the floors look better.
Core Components and Mechanisms
The system’s core mechanism presses flooring panels’ edges downward. This creates a distinctive bevel where the decor layer and texture run all the way to the deepest point. This new approach tackles several key aspects:
- Panel edge formation with continuous decor layering
- Downward pressing mechanism for precise bevel creation
- Texture continuation throughout the bevel depth
Integration with Unilin Division Technologies
The system blends naturally with standard slab production and panel finishing processes. On top of that, this technology builds on our original patents from 2011. It works perfectly with existing Unilin locking systems. This integration solves common manufacturing problems like misaligned bevels and high scrap rates that used to drive up production costs.
Unilin Technologies: Advanced Material Processing Capabilities
Through collaboration with KONO equipment manufacturers, we’ve substantially improved our material processing capabilities. The specialized equipment lets us control bevel depth and alignment precisely, which improves the overall product quality. The system also processes the edges to get rid of sharp surfaces, so they feel better to touch.
These advanced processing capabilities do more than just improve looks. The technology keeps the decor layer intact throughout the pressing process. This means the finished product lasts longer and looks just like natural wood flooring.
Unilin Technologies: Manufacturing Process Innovation
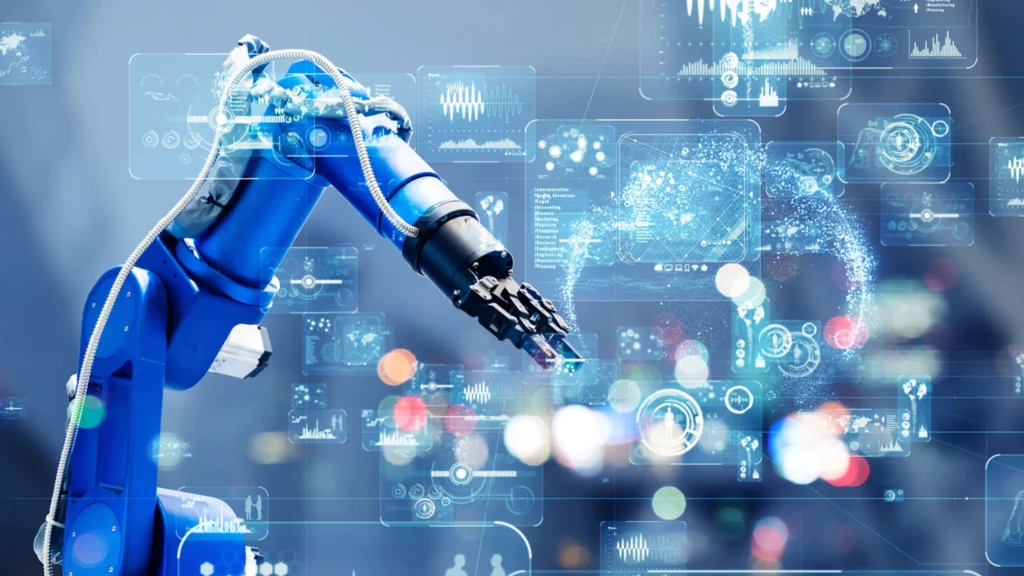
We worked with Chinese manufacturer KONO to create specialized equipment that solves long-standing problems in pressed bevel production.
KONO Equipment Specifications
The KONO machinery comes with patented processing features that work with standard slab production methods. This equipment fits smoothly into existing production lines without changing current manufacturing setups. The system tackles common pressed bevel manufacturing challenges and focuses on bevel alignment accuracy and depth control.
Production Line Optimization
Our improvements to the production line have reduced scrap rates that used to drive up manufacturing costs. The process delivers better bevel alignment while keeping panel finishing consistent. These improvements go beyond just making things faster – manufacturers can create deep and accurate pressed bevels as soon as they install the equipment.
Quality Control Systems
Our manufacturing process quality assurance covers several key areas:
- Automated inspection systems for dimensional accuracy
- Digital monitoring of bevel alignment precision
- Continuous assessment of surface finish quality
The quality control process follows strict standardized procedures. This organized approach helps catch potential defects early and ensures product quality stays consistent throughout manufacturing. These measures have proven to work well in maintaining Unilin flooring products’ reliable locking performance.
Performance Metrics and Testing of Unilin Technologies
Quality assurance in our pressed bevel system relies on exact measurements and thorough testing.
Bevel Precision Measurements
Our system follows tight tolerances for bevel configurations, ranging from 0.1mm to 0.2mm for engineered flooring with thinner top layers. Micro-bevel specs reach about 0.6mm depth to ensure consistent edge quality. Quality machinery can produce bevels as small as 1mm, while lower-grade equipment leaves gaps between 2 to 4mm.
Durability and Stress Testing
We run complete stress tests that check several performance factors:
- Material elasticity and flexural strength
- Cyclic loading resistance up to 100 million reversals
- Environmental condition responses
- Torsional and shear stress tolerance
We tested structural integrity by pushing components to their defined limits. Our team analyzes key performance traits through mesh process simulation without extensive prototyping.
Production Efficiency Analytics
Several critical metrics in the system’s performance monitoring determine operational excellence. We track processing speed under heavy loads through response time measurements. Throughput analysis shows transaction volumes in specific timeframes. CPU, memory, and network usage patterns become clear through resource utilization tracking.
The manufacturing process shows improved efficiency with optimized machining parameters. Our quality control systems keep strict standards, as automated inspection systems watch dimensional accuracy constantly. These analytics work together to measure time savings and production metrics accurately, proving the system’s superior performance in ground applications.
Unilin Technologies: Implementation and Integration
The pressed bevel system just needs careful attention to installation, calibration, and operator expertise to work successfully.
Unilin Flooring Installation Requirements
You can float-install this system on existing floors, which makes it perfect for DIY projects. The special milling technique combines smoothly with existing milling machines. The system lets you complete installation quickly, and you can use your floor within 24 hours.
Equipment Calibration Guidelines
Precise bevel production depends on proper calibration. The system works under these standard reference conditions:
- Temperature managed to keep at 20°C (68°F)
- Barometric pressure at 101,325 Pa
- Water vapor pressure at 1,333 Pa
- CO2 content of air at 0.03%
Bevel alignment and depth accuracy are the foundations of the calibration process. The equipment needs thorough inspection before taking readings at different angles. The system monitors and adjusts parameters until it achieves proper calibration to deliver optimal performance.
Unilin Technologies: Operator Training Protocols
Our training program has both theoretical knowledge and hands-on experience. State-of-the-art facilities with fully functional machine labs support the curriculum. Operators learn about:
- Software operation and maintenance procedures
- Best practices for equipment handling
- Quality control measures
- Troubleshooting techniques
Operators get certification proving their competence after completion. The program offers customized sessions that match specific production requirements. The program stands out with its ongoing support through video instruction and extensive software help systems.
Conclusion
Our latest pressed bevel system represents a major leap forward in flooring manufacturing technology. We partnered with KONO equipment manufacturers to solve persistent issues in SPC flooring production. The system excels especially when you have bevel alignment challenges and need to cut down on scrap rates.
The technical design creates precise edge formation and maintains continuous decor layering through the bevel depth. Our extensive testing shows exceptional strength, with cyclic loading resistance reaching 100 million reversals. This ensures the product’s durability and structural integrity.
The system brings remarkable gains in manufacturing efficiency. Quality control systems keep dimensional accuracy within 0.1-0.2mm tolerances to deliver consistent product quality. A detailed operator training program and calibration guidelines help plants implement the system naturally.
This breakthrough in pressed bevel technology builds on Unilin Technologies’ proven success story, with our portfolio of 3,800 patents backing it up. The system merges with existing production lines to deliver superior esthetics and performance. These features make it the life-blood of future flooring manufacturing.