Industrial laser sales reached a staggering $21.85 billion in 2023, which shows arduous laser technology is growing dominance in modern manufacturing. This revolutionary technology has revolutionized production processes and reduced operation times from hours to minutes while making manufacturing more precise.
Lasers and laser beam systems are reshaping manufacturing capabilities in remarkable ways. The technology makes intricate designs possible that were previously out of reach, streamlines operations, and reduces material waste. These improvements lead to substantial cost savings. Manufacturing companies of all sizes, from automotive to aerospace, find this precision-driven approach a great way to drive innovation.
My complete analysis will show how arduous laser technology revolutionizes manufacturing precision. We’ll get into its core components and assess its effect on production efficiency. The discussion includes integration challenges, quality control measures, and the return on investment businesses can expect from implementing this technology.
Understanding Arduous Laser Technology Fundamentals
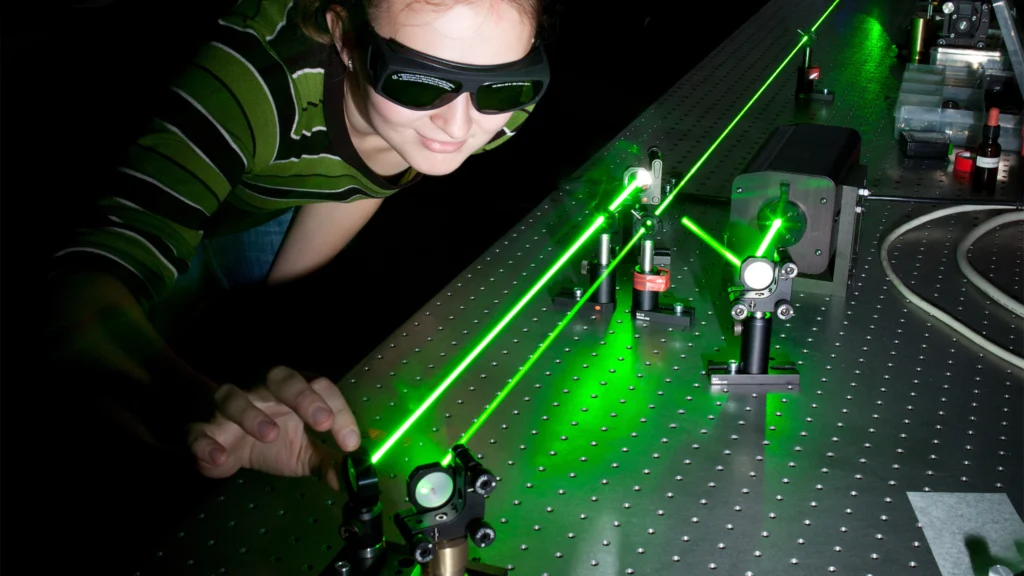
Light Amplification by Stimulated Emission of Radiation (LASER) are the foundations of arduous laser technology. This technology operates through a sophisticated interplay of physical principles and makes use of stimulated emission. Excited atoms release photons in a controlled manner to create a concentrated beam of light.
Core Components and Operating Principles
Three fundamental components work in harmony at the heart of arduous laser technology. The gain medium serves as the material where stimulated emission occurs and can be solid, liquid, or gas-based. The energy source, or pump, energizes the gain medium through electrical current or optical means. The optical feedback mechanism, typically comprising mirrors, creates a resonant cavity that amplifies light.
The gain medium achieves population inversion – a state where more electrons exist in higher energy levels than lower ones. This mechanism creates coherent light with unique properties of monochromaticity and directionality.
Evolution of Precision Laser Systems
Laser systems have seen remarkable advancement since their creation. Sophisticated laser systems enable better precision at faster production rates while using fewer materials and resources. These systems have become vital in demanding sectors like automotive and aerospace manufacturing.
Advanced control systems integration stands out as a notable improvement. Precise coordination between laser firing/modulation and scanner motion has substantially enhanced material processing capabilities. This advancement gives uniform laser density delivery that maintains homogeneous material properties.
Arduous Laser Technology: Key Technological Breakthroughs in 2025
The year 2025 marks substantial progress in laser technology advancement. Ultrafast lasers deliver exceptional precision with minimal heat-affected zones. Green lasers have opened new possibilities to process reflective materials like copper and brass.
A groundbreaking achievement in 2025 showcases the exceptional capabilities of Ba₃(ZnB₅O₁₀)PO₄ (BZBP), a transparent crystal that remains stable under pressures up to 43 Gigapascals – approximately 400,000 times greater than Earth’s atmospheric pressure at sea level. This development expands laser systems’ potential applications in extreme environments, particularly in deep-space exploration and high-energy physics experiments.
Precision Enhancement Mechanisms of Arduous Laser Technology
Three interconnected mechanisms work together in laser technology to achieve exceptional manufacturing accuracy. These mechanisms create a combined effect that raises manufacturing precision to new levels. The system works better as a whole rather than focusing on individual parts.
Beam Quality Optimization
The M2 factor measures beam quality and shows how well a laser performs. A perfect beam quality has a value of 1 when compared to an ideal Gaussian beam. Quality beams offer these benefits:
- Tighter focusing capabilities
- Smoother wavefronts
- Better phase correlation across beam profiles
High beam quality is vital for applications that need strong focusing, especially in cutting and remote welding operations. The beam parameter product (BPP) gives us another key quality measure by multiplying the beam radius at the waist with the far-field beam divergence angle.
Advanced Control Systems
Position Synchronized Output (PSO) technology changes how we control lasers by keeping spot overlap consistent throughout motion profiles. This technology ensures stable laser fluence along the path, whatever the system dynamics might be.
Power correction mapping helps maintain processing quality across the field. The system controls laser power output through analog controls and creates constant fluency at the target material.
Arduous Laser Technology: Real-time Calibration Technologies
A new real-time drift correction method has improved laser-based measurements. This method uses spectral correlation with a revolving in-line gas cell. The approach reduces external drift effects and removes sample and reference signal crosstalk.
Three sub-cells sit in an axially symmetric pattern in the calibration system. This setup achieves a full width at half maximum of 0.2 cm−1 for the target absorption line. The system needs consistent atmospheric transmission and optical alignment during cell revolution to work properly.
Automated monitoring and recalibration features have shown great results. Maximum deviation errors now stay at 3.9 µm within a 30 mm x 20 mm scan field. This level of precision matches the positioning accuracy of mechanical axes at 1.11 µm.
Arduous Laser Technology: Implementation in Manufacturing Processes
Laser technology implementation requires careful attention to integration, safety protocols, and financial aspects. Manufacturing facilities worldwide now adopt these advanced systems to boost their production capabilities while following strict safety standards.
Integration with Existing Production Lines
Adding laser systems to current production lines needs careful evaluation of structural constraints and output targets. Manufacturers must think over production flow optimization and space utilization before installation. We focused on automated systems because 2D laser cutting machines work best when fully automated.
Modern laser systems combine smoothly with existing setups and feature low power consumption with minimal spare parts. These systems work without human interaction once configured correctly and streamline the manufacturing process. A modular approach allows gradual automation of production processes.
Worker Training and Safety Protocols
Worker safety remains the top priority in laser implementation. The Occupational Safety and Health Administration (OSHA) sets specific standards for laser hazards in general industry. These protocols include:
- Mandatory laser safety training certification
- Implementation of controlled access areas
- Installation of proper safety interlocks
- Regular maintenance and inspection schedules
- Specific eyewear requirements for different laser classifications
Training programs cover both simple operations and advanced applications. Expert instructors lead sessions in state-of-the-art facilities to ensure operators get practical experience with the equipment. Classes stay limited to six students to maintain an effective instructor-to-student ratio.
Cost-Benefit Analysis
Financial implications of laser technology go beyond the original investment costs. Laser systems reduce material waste and minimize errors in brownfield jobs to sub-1% levels through improved efficiency. Manufacturers report possible reductions of 2% to 5% in total installed costs for brownfield or revamp capital projects.
The technology shows its cost efficiency in several ways. Laser scanning helps contractors respond better to mid-project changes and reduces expensive modifications and delays. The long-term benefits often justify the substantial initial investment through increased productivity and lower operational expenses.
Companies see returns through faster project completion times and better product quality. Medical device manufacturing has showed significant cost savings through improved precision that reduces post-processing requirements.
Quality Control and Measurement Systems
Modern manufacturing just needs precise quality control systems to maintain high standards. Laser technology comes with sophisticated measurement and inspection capabilities that boost production accuracy.
Automated Inspection Technologies
Advanced laser inspection systems use CCD cameras and CMOS sensors for immediate monitoring. These systems reach remarkable precision and detect surface defects at microscopic levels. The beam sizes can adjust to one-thousandth of a millimeter. A single pass of the inspection process covers more than 7 inches and generates thousands of data points.
The measurement system uses quadrant-photodetectors (QPD) that deliver theoretical resolutions of:
- 0.1 μm for horizontal and vertical measurements
- 0.25 arcsec for angular measurements
- 0.17 arcsec for rotational precision
Error Detection and Correction
A sophisticated beam-splitting process powers the error detection mechanism. The transmitted beam splits into two components. One beam measures horizontal and vertical deviations while the other tracks rotational variations. The system achieves maximum residual measurements of ±0.7 μm at original positions and ±0.9 μm at final positions within a ±100 μm calibration range.
Immediate calibration technologies keep accuracy consistent through automated drift compensation. The system spots anomalies automatically, including missing components, incorrect material types, and dimensional variations. This automated approach ended up reducing inspection times and removed the need for additional laboratory analysis.
Data Analytics for Quality Assurance
Quality data storage systems record and analyze process information from lasers, optics, and sensor systems in sync. Manufacturers can use the collected data to:
- Track component-specific process parameters
- Analyze trends across multiple production runs
- Find mechanisms of quality deviations
Machine learning algorithms trained on historical quality data can spot subtle changes in process parameters that might indicate potential risks. The system keeps quality records locally and will give a secure data management while making shared traceability of manufacturing processes possible.
These quality control mechanisms’ integration showed most important improvements in manufacturing precision. Optical measurement techniques avoid mechanical contact with analyzed parts and deliver reliable results while preserving component integrity. This contactless approach needs minimal maintenance and keeps performance consistent over long periods.
Arduous Laser Technology: ROI and Performance Metrics
Manufacturing facilities using arduous laser technology show substantial returns on investment across multiple performance metrics. These laser systems deliver remarkable gains in both operational costs and production quality.
Productivity Improvements
Arduous laser technology speeds up manufacturing processes and reduces operation times from hours to minutes. Laser processing systems complete sophisticated shapes and patterns with unique accuracy in minutes. The technology cuts 50 to 100 times faster than traditional wire cutting methods.
Manufacturing facilities see increased efficiency through:
- Shorter cycle times and less maintenance
- Simplified processes with fewer redundancies
- Exceptional accuracy in repetitive tasks
Arduous Laser Technology: Cost Reduction Analysis
Arduous laser technology’s financial benefits show up in multiple ways. Manufacturers see a 50% drop in manufacturing costs right away. The photoelectric conversion rate reaches 40%, while traditional CO₂ lasers achieve only 10% efficiency.
Cost savings come from several areas. Laser systems work without tool wear and tear, which means minimal maintenance. The technology also cuts production waste through accurate treatments, almost eliminating material wastage. Companies can cut operational expenses by up to 50% by using compressed air instead of expensive gasses like oxygen or nitrogen.
Quality Enhancement Statistics
Quality metrics show major improvements with laser implementation. While original alignment can be challenging, proper laser tracker alignment delivers remarkable precision. The technology maintains steady performance with minimal deviation errors of 3.9 µm within a 30 mm x 20 mm scan field.
Quality improvements go beyond precision metrics. Laser-assisted machining performs better at cutting than conventional methods. The process helps save energy by reducing cutting force while maintaining green machining standards.
Laser technology in manufacturing works exceptionally well in specific sectors. Medical device manufacturing shows substantial cost savings through better precision. Product recalls cost around USD 10 million each, but laser technology’s precise manufacturing capabilities can help reduce these quality-related expenses.
Conclusion
Arduous laser technology has become a game changer in modern manufacturing. It doubles precision and substantially cuts operational costs. Our complete analysis shows how sophisticated beam quality optimization and immediate calibration technologies achieve remarkable accuracy levels of 3.9 µm within standard scan fields.
Manufacturing facilities using this technology see major benefits. A 50% reduction in manufacturing costs and 40% photoelectric conversion rate prove its efficiency. Automated inspection systems, advanced error detection mechanisms, and quality control measures help maintain exceptional standards throughout production.
The technology’s effects go beyond precision metrics. Worker safety protocols, training programs, and automated monitoring systems create a safe and efficient operation. Quality assurance analytics help manufacturers learn about their processes to optimize and prevent defects continuously.
The future looks promising for arduous laser technology in manufacturing beyond 2025. Ultrafast lasers and breakthrough materials like BZBP crystals create new possibilities for extreme environment applications. These advancements, combined with proven ROI metrics and boosted productivity rates, make arduous laser technology a vital tool for manufacturers who want precision, efficiency, and an edge over their competition.